Septic Building Permit Application Information
Introduction
On-site sewage systems are regulated by the Ontario Building Code, O. Reg. 332/12 made under the Ontario Building Code Act, S.O. 1992, c. 23 subject to the following conditions:
- The total daily design sanitary sewage flow must not exceed 10,000 litres per day; and
- The on-site sewage system, and all building(s) the system serves, must be located on the same parcel of land.
This information package is intended as a guide for completing your application for a sewage system permit. Be advised that the Building Code Act and the Ontario Building Code take precedence over any discrepancies in this information.
No person shall construct, repair, alter install or perform any work on a sewage system unless a building permit has been issued.
Classes of Sewage Systems
Class 1
A sewage system that is used for the disposal of human body waste without added water. No permit is required for the construction of a Class 1 sewage system.
Examples include: earth pit privy (outhouse), composting toilet (no overflow), and privy vault. Note: Ontario Building Code and zoning provisions do apply to Class 1 systems, even though a permit is not required.
Class 2
A sewage system that is used for the disposal of greywater from sinks, tubs, showers, or laundry units. Commonly known as a leaching pit.
Permit Required: Yes, for the construction of a Class 2 sewage system.
Class 3
A sewage system that is used for the disposal of human body wastes from another type of sewage system, such as overflow waste from a composting toilet. Commonly referred to as a cesspool.
Permit Required: Yes, for the construction of a Class 3 sewage system.
Class 4
A sewage system that is used for the disposal of domestic sewage. The system includes a treatment unit and leaching bed (e.g. septic tank and filter bed).
Permit Required: Yes, for the construction of a Class 4 sewage system.
Class 5
A sewage system that is used for the disposal of domestic sewage, consisting of a holding tank for the retention of sewage, to be emptied by a licensed sewage hauler.
Permit Required: Yes, for the construction of a Class 5 sewage system.
Documents Required
- Completed Application: Ensure the application form is filled out in its entirety.
- Authorization by Owner: If someone other than the property owner is submitting the application, written authorization from the owner is required.
- Floor Plans: Provide floor plans for all levels of the building, including the basement, with identification of all rooms, washrooms, and the number of plumbing fixtures.
- Site Plan: A detailed, legible site plan drawn to scale that includes the information below.
Sewage System Site Plan Requirements
To minimize delays in the issuance of the permit, ensure that your site plan includes the following details:
- Lot Size and Dimensions: Clearly label the dimensions of the property.
- Location of Buildings: Indicate the locations of all existing and proposed buildings, and note their intended use.
- Location of Decks and Accessory Buildings: Include both attached and detached structures
- Waterbodies: Identify the location and name of all nearby waterbodies.
- Wells: Mark the type and location of all wells, including those on neighbouring properties.
- Setbacks: Provide setback distances for the following:
- Proposed septic tank and leaching bed from buildings, decks, and accessory structures.
- Distance from waterbodies to the sewage system.
- Setback from overhead hydro lines (minimum of 4.8 metres).
- Distance from wells in proximity to the sewage system.
- Mantle and Flow Direction: If applicable, show the location and direction of the mantle and flow.
- Driveway, Parking and Vehicle Movement Location: Mark the location of the driveways and any vehicle movement areas.
- Street name: include the names of any adjacent streets or roads.
- Sewage Systems: Identify sewage systems (if any) on adjacent properties, including tank and bed locations.
- Multiple Sewage Systems: If more than one sewage system exists on the property, show the locations of all systems, including tank and bed locations.
- Foundation Drainage: Show the location of foundation drainage outlets
- Downspout Discharge: Indicate the location of eavestrough downspouts and their discharge points.
Ensure that the site plan is clear and accurate, as this information will help expedite the review and approval process for your sewage system permit application.
Septic Tank System:
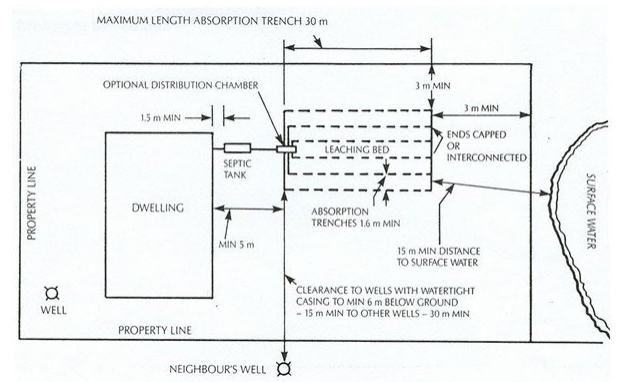
Notes:
- Show location of any proposed drywell pits and trenches from the dwelling
- Note the type of well (for property of owner and neighbour)
- Location of tank and leaching bed to be on lower ground than adjacent wells or springs, if possible.
- Internal plumbing and main drainage outlet should be designed with consideration of possible future connection to sanitary sewers.
- Roof water, surface water, discharge from footing drains, etc., must be diverted to eliminate entry to septic tank.
- Leaching beds are NOT to be located in swampy ground or in ground prone to flooding.
- See the Regulation regarding details for the siting of the septic tank and tile bed.
Sewage system components must meet the minimum horizontal clearance distances as outlined in the OBC tables listed:
Table 8.2.1.6.B.
Table 8.2.1.5.
Completing the Application
-
- Complete the Ministry of Municipal Affairs and Housing application form and Schedule 2 - Septic Installer Information form.
- Ensure all information is completed on the forms and that it is dated and signed by the applicant.
Authorization Forms Required for Application
If you are applying on behalf of someone else or an organization, certain forms are required:
-
- If you are applying on behalf of a private property owner, you must complete and upload the Authorization to Act as Agent form.
- If applying on behalf of an organization, you must complete and upload the Representation and Warranty form.
Designer and Installer Information Forms
Schedule 1: Designer Information Form
Who Completes This Form?
- This form must be completed in its entirety and refers to the designer of the sewage system, not the building.
- Property Owners: If you are designing your own sewage system, you are exempt from registration and qualification as a designer under O. Reg. 332/12, Div. C, Part 3.
- Installers as Designers: If the installer is providing the design for their own installation, they will be listed as an "other designer."
Schedule 2: Sewage System Installer Form
Who Completes This Form?
- This form must be completed by a Qualified Sewage System Installer and signed by the property owner or their authorized agent to authorize the work.
- The Building Code Identification Number (BCIN) of the installer must be provided.
Property Owner Installation:
-
- If the property owner is installing the system themselves, only Sections A, B, and E need to be completed.
- In Section B, select the middle box (“No”) to indicate that the property owner is not engaged in the business of constructing sewage systems.
Septic Design Considerations
When designing a septic system, several key factors contribute to the calculation of the system's required capacity. The designer must carefully consider these factors to determine the Total Daily Design Sanitary Sewage Flow and ensure the system can properly handle the volume of waste generated by the property. Below are the main considerations:
1. Total Number of Plumbing Fixtures
Each plumbing fixture or group of fixtures is assigned a specific volume (called "fixture units"). The designer must:
- Count all plumbing fixtures, including rough-ins, on the property (e.g., toilets, sinks, bathtubs, showers, dishwashers, etc.).
- Multiply the number of each fixture by the volume assigned to it to calculate the total volume for all fixtures.
This volume contributes to the Total Daily Design Sanitary Sewage Flow (Q).
2. Total Number of Bedrooms
The total number of bedrooms on the property is a critical factor in septic design. All bedrooms within the dwelling unit, including those in the main floor, upper stories, and basement, must be counted. Additionally, lofts, dens, office spaces, playrooms, and any other rooms that could potentially be used as bedrooms should also be counted as bedrooms for the purpose of septic design.
3. Finished Area
The total amount of finished area on the property, including both the primary dwelling and all outbuildings (e.g., sleeping cabins, garage lofts, sunrooms, etc.), must be included in the design considerations. The area of a basement that is fully below grade is typically excluded from the finished area calculation.
4. Total Fixture Units
The total fixture units represent the sum of all fixture units calculated above. This total is used in determining the overall flow requirements for the septic system.
5. Total Design Sanitary Sewage Flow (Q)
The Total Design Sanitary Sewage Flow (represented as "Q" in the formula) is the calculated amount of sewage that the septic system must be able to handle each day. This value is based on the total number of fixture units, bedrooms, and the finished area, and it is used to size the septic tank and leaching bed.
By carefully considering all of these factors, the designer can ensure that the septic system is sized correctly to handle the waste generated by the property, minimizing the risk of system failure or overflow.
Fixture Unit Type | Volume per unit |
---|---|
Water Closets (Toilets) | 4 |
Kitchen sink (Double sink to one trap is one sink) | 1.5 |
Wash Basin (i.e. Bathroom sink) | 1.5 |
Bathtub and/or Shower | 1.5 |
Dishwasher - plumbed separately | 1.0 |
Dishwasher - plumbed through kitchen sink | 0 |
Clothes Washing Machine | 1.5 |
Single or Double Laundry Tub | 1.5 |
Floor Drains - 2" trap | 2 |
Floor Drains - 3" trap | 3 |
Fixture Unit Type | Volume per unit |
---|---|
Water Closets (Toilets) | 4 |
Kitchen sink (Double sink to one trap is one sink) | 1.5 |
Wash Basin (i.e. Bathroom sink) | 1.5 |
Bathtub and/or Shower | 1.5 |
Dishwasher - plumbed separately | 1.0 |
Dishwasher - plumbed through kitchen sink | 0 |
Clothes Washing Machine | 1.5 |
Single or Double Laundry Tub | 1.5 |
Floor Drains - 2" trap | 2 |
Floor Drains - 3" trap | 3 |
See Table 8.2.1.3.A. of the Ontario Building Code for specifics volumes for occupancies.
Notes for Table 8.2.1.3.A:
1.The occupant load shall be calculated using Subsection 3.1.17.
2. Where multiple calculations of sewage volume is permitted the calculation resulting the highest flow shall be used in determining the design daily sanitary sewage flow.
3. Total finished area, excluding the area of the finished basement.
For all other occupancies, the total daily design flow rate shall be at least the value as stated in Column 2 from Table 8.2.1.3.B of the Ontario Building Code.
Site Expectations
First Visit/Test Holes
Before calling for the required inspection, the following tasks must be completed:
-
Test Holes:
- Two test holes must be dug to a minimum depth of 1.5 meters.
- The test holes should be placed at least 5 meters apart and within the proposed leaching bed location.
- Steps should be dug in the test holes to allow safe entry, if necessary.
-
Identifying the Septic Bed Area:
- Clearly mark the area of the septic bed on-site using one of the following methods:
- Spray paint on the corners of the proposed bed area.
- Mark the location of the proposed well, if known.
- Clearly mark the area of the septic bed on-site using one of the following methods:
-
Protection of Test Holes:
- Open test holes should be covered to prevent rainwater from entering.
- The test hole locations should be clearly marked and protected to prevent accidents.
Field Inspection of Sewage System Prior to Backfill
An “As Built System” layout must be submitted during the permit application process. Any changes to this layout during the process will need to be submitted to Building Services for review before installation.
Building Services Inspectors require 48 hours notice prior to the required inspection.
For the final inspection before backfilling the system, the following criteria must be met:
Submission of As-Built Layout:
- Submit the As-Built System layout, including any changes made during the process.
Pumps (if used):
- If pumps are used, include the make and model on the As-Built design.
Tank Details:
- The volume and manufacturer's markings of the septic or holding tank must be clearly visible.
- The top of the tank must not be backfilled during inspection.
Access to Tank Lids:
- Tank lids must be accessible for inspection. If any special tools or bits are required to remove the lids, they must be provided or left on-site for the inspector.
Visibility of Piping:
- All distribution and header piping must be clearly visible and not backfilled during inspection.
Compacted Base for Piping:
- All header piping must be located on a compacted base.
Distribution Boxes:
- Distribution boxes (if used) must not be backfilled and must be located on a compacted base.
Piping and Tracer Wire:
- The corners of the bed and each run of distribution piping must be pinned with metal stakes or lined with Tracer wire for future detection.
- All buried piping or forcemains outside the leaching bed area must be lined with Tracer wire, in accordance with the Ontario Building Code.
Approval of Design Changes
- Any changes to the design or system component locations must be approved by the Building Department before the final inspection.
By adhering to these expectations and completing the required steps, the installation process will proceed efficiently, ensuring compliance with local regulations and standards.
Soil Types
When designing a sewage system, understanding the soil conditions is crucial for ensuring the system's effectiveness and longevity. Below are the key soil considerations and requirements that must be observed on-site.
Test Holes
Number of Test Holes:
- A minimum of two test holes must be dug on-site to a depth of at least 1.5 meters.
Spacing of Test Holes:
- The test holes must be spaced at least 5 meters apart to provide a representative sample of the subsoil conditions.
Accessibility for Inspection:
- The test holes must remain open and available for inspection.
- However, to prevent water accumulation and ensure safety, the holes must be covered between excavation and inspection to protect the area from rainwater entering the holes and to avoid accidents on-site.
Soil and Groundwater Considerations
Several factors related to soil depth and water conditions need to be assessed during the test hole process:
-
Depth to Bedrock:
- The distance from the original grade to bedrock must be measured if bedrock is encountered in the test holes.
- This information is vital as a shallow bedrock layer may limit the effective depth for leaching and require special system considerations.
-
Depth to High Groundwater Table:
- The distance from the original grade to the high groundwater table must be determined.
- If the high water table is encountered, it can affect the ability of the system to properly treat and disperse wastewater. This must be taken into account in the design of the leaching bed and system layout.
Percolation Rate
The percolation rate (“T”) is a key factor in the design of the leaching system, as it indicates how well the soil will absorb water. The percolation rate is defined as:
- The average time in minutes it takes for water to drop one centimeter in the soil during a percolation test.
Percolation Test Process:
- A percolation test is typically conducted on-site by introducing water into the test hole and measuring how quickly it is absorbed by the soil.
- If a soils analysis is done instead, the percolation rate will be determined through laboratory testing.
This rate is important because it influences the size and design of the leaching bed. Soils with a fast percolation rate may require a larger leaching bed, while soils with a slow percolation rate may necessitate a more robust treatment system or larger leaching area to prevent groundwater contamination.
By carefully considering the above soil and groundwater factors, the designer can ensure that the septic system is appropriately sized and suited to the specific conditions of the site, reducing the likelihood of system failure and protecting public health and the environment.
Sewage System Design
When designing a sewage system, two critical factors must be determined to ensure the system is properly sized and functions effectively. These factors are:
-
Daily Design Sanitary Sewage Flow (Q):
The daily design sanitary sewage flow, or "Q", represents the total volume of wastewater the system must handle per day. This value is calculated based on factors such as the number of plumbing fixtures, the number of bedrooms, and the size of the property. -
Percolation Rate (T):
The percolation rate ("T") indicates how well the soil absorbs water, measured by the time it takes for water to drop one centimeter during a percolation test. This rate is crucial for determining the size and layout of the leaching bed and ensuring the system can effectively disperse treated effluent into the soil.
Fixture Unit Type | Volume per unit |
---|---|
Water Closets (Toilets) | 4 |
Kitchen sink (Double sink to one trap is one sink) | 1.5 |
Wash Basin (i.e. Bathroom sink) | 1.5 |
Bathtub and/or Shower | 1.5 |
Dishwasher - plumbed separately | 1.0 |
Dishwasher - plumbed through kitchen sink | 0 |
Clothes Washing Machine | 1.5 |
Single or Double Laundry Tub | 1.5 |
Floor Drains - 2" trap | 2 |
Floor Drains - 3" trap | 3 |
See Table 8.2.1.3.A. of the Ontario Building Code for specifics volumes for occupancies.
Notes for Table 8.2.1.3.A:
1.The occupant load shall be calculated using Subsection 3.1.17.
2. Where multiple calculations of sewage volume is permitted the calculation resulting the highest flow shall be used in determining the design daily sanitary sewage flow.
3. Total finished area, excluding the area of the finished basement.
For all other occupancies, the total daily design flow rate shall be at least the value as stated in Column 2 from Table 8.2.1.3.B of the Ontario Building Code.
Site Expectations
First Visit/Test Holes
Before calling for the required inspection, the following tasks must be completed:
-
Test Holes:
- Two test holes must be dug to a minimum depth of 1.5 meters.
- The test holes should be placed at least 5 meters apart and within the proposed leaching bed location.
- Steps should be dug in the test holes to allow safe entry, if necessary.
-
Identifying the Septic Bed Area:
- Clearly mark the area of the septic bed on-site using one of the following methods:
- Spray paint on the corners of the proposed bed area.
- Mark the location of the proposed well, if known.
- Clearly mark the area of the septic bed on-site using one of the following methods:
-
Protection of Test Holes:
- Open test holes should be covered to prevent rainwater from entering.
- The test hole locations should be clearly marked and protected to prevent accidents.
Field Inspection of Sewage System Prior to Backfill
An “As Built System” layout must be submitted during the permit application process. Any changes to this layout during the process will need to be submitted to Building Services for review before installation.
Building Services Inspectors require 48 hours notice prior to the required inspection.
For the final inspection before backfilling the system, the following criteria must be met:
Submission of As-Built Layout:
- Submit the As-Built System layout, including any changes made during the process.
Pumps (if used):
- If pumps are used, include the make and model on the As-Built design.
Tank Details:
- The volume and manufacturer's markings of the septic or holding tank must be clearly visible.
- The top of the tank must not be backfilled during inspection.
Access to Tank Lids:
- Tank lids must be accessible for inspection. If any special tools or bits are required to remove the lids, they must be provided or left on-site for the inspector.
Visibility of Piping:
- All distribution and header piping must be clearly visible and not backfilled during inspection.
Compacted Base for Piping:
- All header piping must be located on a compacted base.
Distribution Boxes:
- Distribution boxes (if used) must not be backfilled and must be located on a compacted base.
Piping and Tracer Wire:
- The corners of the bed and each run of distribution piping must be pinned with metal stakes or lined with Tracer wire for future detection.
- All buried piping or forcemains outside the leaching bed area must be lined with Tracer wire, in accordance with the Ontario Building Code.
Approval of Design Changes:
- Any changes to the design or system component locations must be approved by the Building Department before the final inspection.
By adhering to these expectations and completing the required steps, the installation process will proceed efficiently, ensuring compliance with local regulations and standards.
Soil Types
When designing a sewage system, understanding the soil conditions is crucial for ensuring the system's effectiveness and longevity. Below are the key soil considerations and requirements that must be observed on-site.
Test Holes
Number of Test Holes:
- A minimum of two test holes must be dug on-site to a depth of at least 1.5 meters.
Spacing of Test Holes:
- The test holes must be spaced at least 5 meters apart to provide a representative sample of the subsoil conditions.
Accessibility for Inspection:
- The test holes must remain open and available for inspection.
- However, to prevent water accumulation and ensure safety, the holes must be covered between excavation and inspection to protect the area from rainwater entering the holes and to avoid accidents on-site.
Soil and Groundwater Considerations
Several factors related to soil depth and water conditions need to be assessed during the test hole process:
-
Depth to Bedrock:
- The distance from the original grade to bedrock must be measured if bedrock is encountered in the test holes.
- This information is vital as a shallow bedrock layer may limit the effective depth for leaching and require special system considerations.
-
Depth to High Groundwater Table:
- The distance from the original grade to the high groundwater table must be determined.
- If the high water table is encountered, it can affect the ability of the system to properly treat and disperse wastewater. This must be taken into account in the design of the leaching bed and system layout.
Percolation Rate
The percolation rate (“T”) is a key factor in the design of the leaching system, as it indicates how well the soil will absorb water. The percolation rate is defined as:
- The average time in minutes it takes for water to drop one centimeter in the soil during a percolation test.
Percolation Test Process:
- A percolation test is typically conducted on-site by introducing water into the test hole and measuring how quickly it is absorbed by the soil.
- If a soils analysis is done instead, the percolation rate will be determined through laboratory testing.
This rate is important because it influences the size and design of the leaching bed. Soils with a fast percolation rate may require a larger leaching bed, while soils with a slow percolation rate may necessitate a more robust treatment system or larger leaching area to prevent groundwater contamination.
By carefully considering the above soil and groundwater factors, the designer can ensure that the septic system is appropriately sized and suited to the specific conditions of the site, reducing the likelihood of system failure and protecting public health and the environment.
Sewage System Design
When designing a sewage system, two critical factors must be determined to ensure the system is properly sized and functions effectively. These factors are:
-
Daily Design Sanitary Sewage Flow (Q):
The daily design sanitary sewage flow, or "Q", represents the total volume of wastewater the system must handle per day. This value is calculated based on factors such as the number of plumbing fixtures, the number of bedrooms, and the size of the property. -
Percolation Rate (T):
The percolation rate ("T") indicates how well the soil absorbs water, measured by the time it takes for water to drop one centimeter during a percolation test. This rate is crucial for determining the size and layout of the leaching bed and ensuring the system can effectively disperse treated effluent into the soil.
Design Guidance
-
General Information:
The above factors, Q (daily sewage flow) and T (percolation rate), are foundational in determining the appropriate size and design of the sewage system. However, this information should be treated as general guidance only. -
Qualified Professionals:
For a properly designed sewage system, it is highly recommended that property owners consult with a qualified designer and installer. They will apply the information to create a custom design that meets the specific needs of the property and complies with regulatory requirements. -
Role of the Inspector:
It is important to note that inspectors are not authorized to design sewage systems. The responsibility for designing the system lies with the property owner, agent, installer, design consultant, or engineer. The design must comply with Part 8 of the Ontario Building Code (O. Reg. 332/12), which governs the installation of sewage systems.
Applications for new septics, expansions or repairs to existing septic systems will be submitted through email at residentialpermits@peterborough.ca.
Contact Us
City Hall
500 George St. N.
Peterborough, ON
K9H 3R9
Phone: 705-742-7777
Toll Free: 1-855-738-3755
Email Us